Case Study
An Aerial Perspective:
UAS Roofing Inspection
With help from our partners:
Sain Engineering Associates, Inc and Nova Consulting:
The safer, faster, cheaper way to identify and report structural damage.

Overview:
Roofs keep our buildings dry and comfortable. Despite their importance, roofs don’t always get their due attention. Accurate and comprehensive reporting throughout the lifespan of a roof can save money in the long-term and provide building owners and occupants with priceless peace-of-mind. This case study focuses on the application of sUAS to identify structural damage to buildings and the data management techniques that can be used to maintain records of inspections.
Economic Significance:
Consider a single-family housing unit with 5,000 square-feet of roof, designed for a 20-year lifespan. Installation costs are about $5 per square foot including material and labor (possibly more if you factor in removal of old roof), which means that roof’s installation cost is about $25,000. Based on the 20-year average lifespan, the average accrued cost per year of your installed roof is $1,250. If the roof is not properly installed in the first place, or maintained, and it only lasts half of it’s expected life (say, only 10-years), the yearly accrued cost of this roof doubles to $2,500 a year. Roofing experts suggest that proper roof maintenance should budget 2% of the installation costs, per year, making good maintenance at or under $500 per year per unit in this case, a no-brainer. An accrued annual cost of $1,750 is preferable to $2,500 or worse.

Severe shrinkage and weathering of asphalt shingles. Eventually the flaps begin to tear away, exposing the nails underneath. Once the nail heads are exposed, water running down the roof can leak into interior spaces.
Our Mission:
Given the need for comprehensive roof reporting for developers, construction companies, homeowners and insurers, we developed our pilot training program and sUAS roofing inspection solution to meet the needs of the industry. We can provide a customized inspection solution that best fits the needs of individual roofs as well as community size, even if those needs change across your site. Our clients value making better informed decisions, and also providing cost-saving solutions to their stakeholders.
Challenge:
A developer just wrapped up construction on a large residential community in northern New Jersey. The project included new construction for 46 residential units and a large clubhouse, each with an individual footprint of roughly 8,000 square feet. Within a few months of finishing construction, residents across the development began complaining of water leaks in their new roofs. The developer investigated and then sued the general contractor, who settled for $7.4 million. With the money won in the court case, an engineering team (Sain Engineering Associates Inc., working together with Nova Consulting) was brought in for subject matter expertise, to assess the damage and submit a proposal for managing repairs. This engineering team hired Tenbo Air to provide a comprehensive inspection of each unit, and a database to help identify, document, and archive the damaged units.
The Process:
1
A dedicated Tenbo Air Project Manager conducts a site evaluation. Evaluations can consist of satellite analysis and/or an on-site visit depending on project location and complexity.
2
Based on the results of the site evaluation, a set of flight plans are tailored for site-specific features. These flight plans combine custom and automated missions to ensure that the desired roof surfaces and angles are covered.
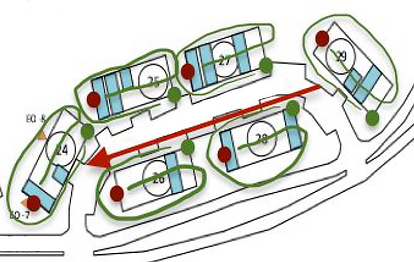
3
On the planned inspection day(s), internally trained and FAA part-107 certified sUAS pilots and trained field engineers arrive on site to capture high-resolution RGB imagery data covering all areas of interest.
4
Back at HQ, the RGB imagery data covering the project site are reviewed and organized by our analysts. The optimally organized raw footage is packaged and uploaded to the cloud.
5
Next, the close-up RGB images of the roof are organized according to location neatly into a folder architecture that intuitively reflects the inspection site(s) (i.e. site number, building name, etc).
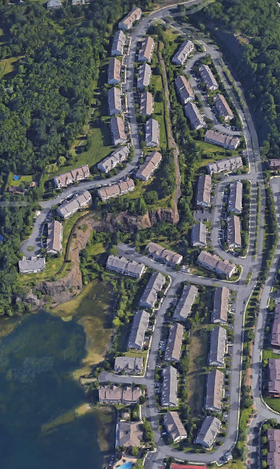


6
Geotagged images are used to create an interactive map with easy-to-use viewing and sharing capabilities. These maps can be easily linked to operational stakeholders and can be used by project managers in the field to more quickly and specifically orient and direct workers.
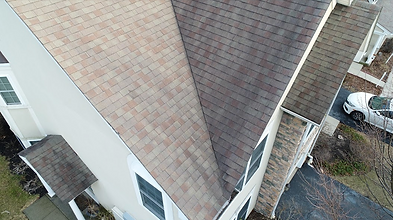

7
Finally, Tenbo Air writes and delivers a final report to the engineering team leads. This report details the project requirements, explains the specific methods used in the field, and catalogs the specific deliverable assets for posterity.
Solutions & Results:
Data Acquisition Method:
-
Close-proximity, high-density, and high-resolution (20mp) photo documentation of roofs via unmanned aerial system (UAS)
Execution Timeframe:
-
½ day: remote site inspection and preliminary project planning, field crew briefing
-
1 day: in-person site reconnaissance and field work planning
-
2 days: aerial inspection data collection (2 pilots working simultaneously)
-
4 days: data organization, map creation, report generation, final delivery
-
Total turnaround time for the project: 7½ days
Download the Case Study PDF:
